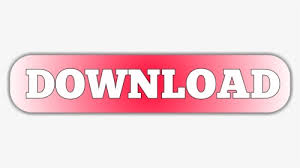
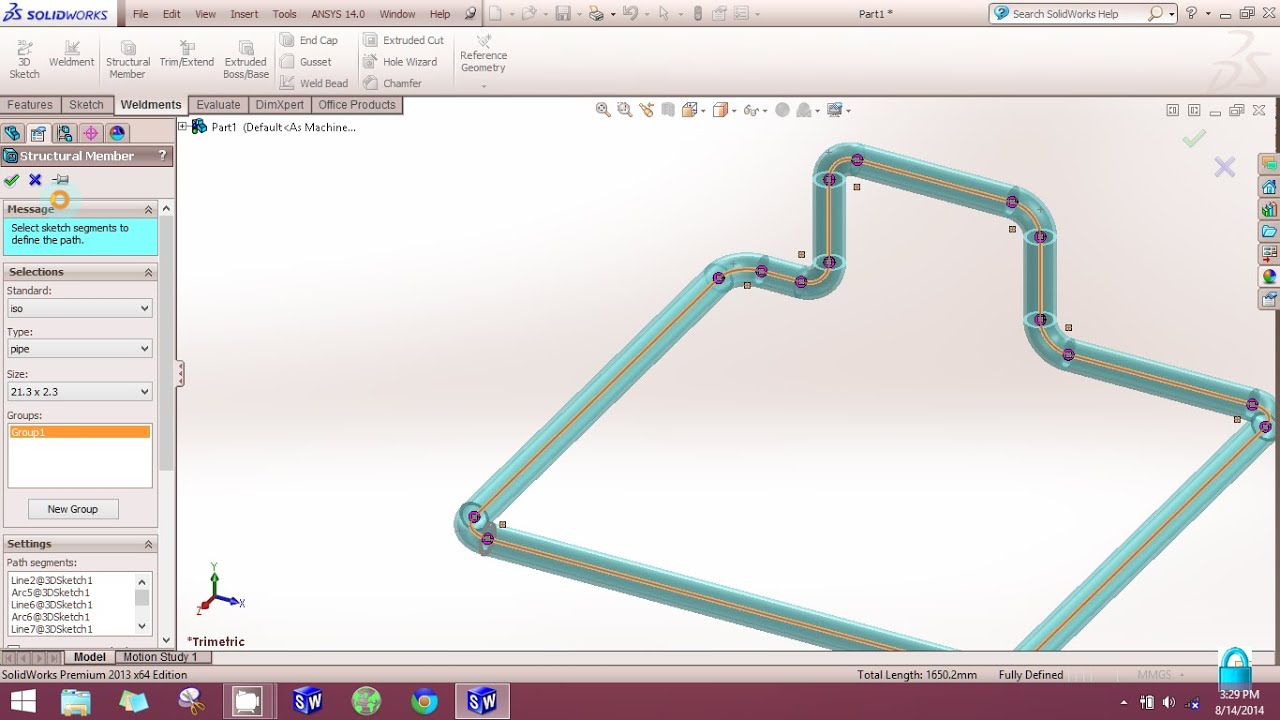
2004 Even-Ram and Yamada 2005 Zaman et al. In contrast to experiments with cells grown in 2-dimensional monolayers, 3-dimensional cell culture systems allow for the construction of microenvironments characterized by preservation of native cell-cell and cell-matrix interactions ( Abbott 2003). The micro-environment may include specific cell populations, extracellular matrix components, and soluble or immobilized chemical signals. In vitro systems designed to study these cellular behaviors rely on the replication of local microenvironments, including the presentation of relevant stimuli in an appropriate spatiotemporal pattern. 2008) depend on the directed movement or transcriptional response of cells to biochemical and biophysical stimuli. 2008), inflammation ( Friedl and Weigelin 2008), and cancer metastasis ( O’Hayre et al.

Many important biological processes such as gastrulation and organogenesis ( Montero and Heisenberg 2004 Laird et al. Additionally we show the effect of concentration gradients of the morphogen Sonic hedgehog on the specification of differentiating neural progenitors in a 3-dimensional matrix. We demonstrate the ability of the new device to quantitate chemotactic responses in a variety of cell types, yielding a complete profile of the migratory response and representing the total number of migrating cells and the distance each cell has migrated. Pressure gradients between the source and sink wells are dissipated through low resistance channels in parallel with the gel channel, thus minimizing the convection of solute in this region.
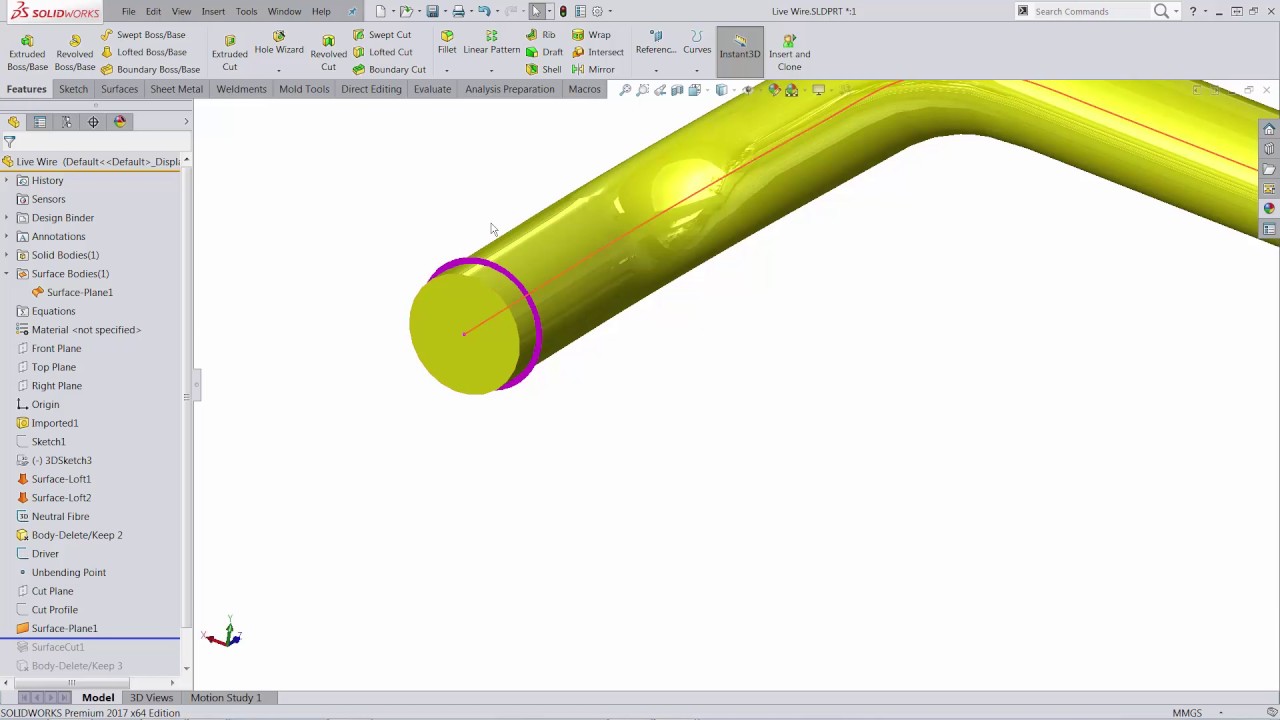
Here we describe a new microfluidic device which employs a parallel arrangement of wells and channels to create stable, linear concentration gradients in a gel region between a source and a sink well. Many approaches have been developed to create gradients of soluble factors, but the complexity of such systems or their inability to create defined and controllable chemical gradients has limited their widespread implementation. Although we still do work in all industries, our largest customer sales are for the medical device, medical equipment, medical disposables, and medical contract manufacturers.The advent of microfluidic technology allows control and interrogation of cell behavior by defining the local microenvironment with an assortment of biochemical and biophysical stimuli.Our Moldmakers / Toolmakers / Tool Shops: These have the latest equipment and capabilities for serving your needs.Your product's life starts with thorough planning in the process of developing its injection molding tooling. We consider the finishing, (machining, decorating), the assembly (manual and automatic), the packaging (for transfer or retail), and the product's end-of-life. Project Lifecycle: We examine the entire lifespan of the product.
FORMED TUBE SOLIDWORKS 2010 FULL
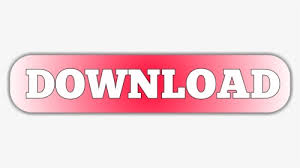